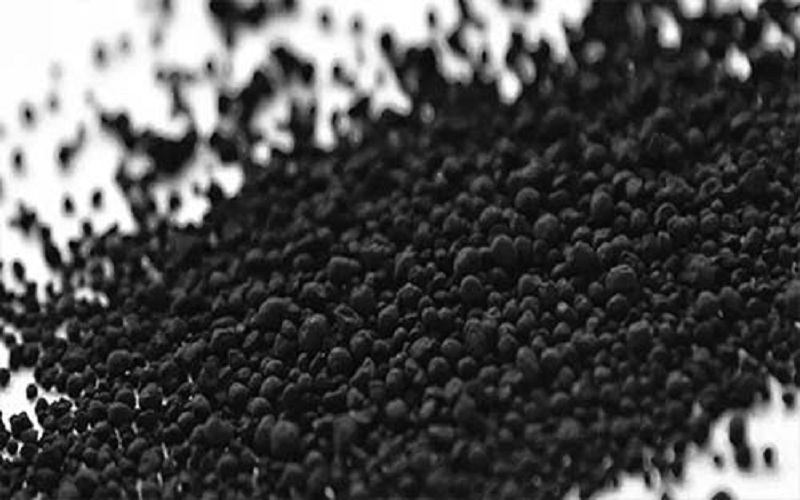
Choosing the right type and quality of recovered carbon black for your needs can seem like a daunting task. With so many options available, it’s easy to get overwhelmed. However, taking some key factors into consideration can help you make an informed decision. Here are 8 important things to keep in mind while selecting recovered carbon black.
1. Application
The application that the recovered carbon black will be used for is a very important consideration when selecting the right type and grade. Carbon black is used across multiple industries for varied purposes. The properties required from the carbon black change depending on what it will be used for.
If the carbon black is meant for tires, the key properties needed are high abrasion resistance and strong reinforcing ability. Tires face a lot of friction and force during rolling. The carbon black used in tires needs to improve the rubber compound’s strength and durability to prevent premature wear. It must withstand the constant abrasion from road surfaces without degrading the tire performance.
On the other hand, if the application is hoses or belts, the focus is more on heat and pressure resistance rather than abrasion. Hoses and belts require carbon black that reinforces the material to withstand high pressures and temperatures experienced during their use. For wires and cables, the carbon black is chosen for its conductivity and electrical properties in addition to mechanical reinforcement.
2. Particle Size and Structure
The particle size, shape and structure of carbon black are important physical characteristics that influence the properties it imparts when compounded with materials. The particle size is measured in nanometers and refers to the average diameter of the carbon black particles. Larger particle sized carbon blacks, around 35-40nm, are able to create more contact surfaces and better interlink the material when compounded. This enhances reinforcement characteristics like tensile strength and modulus.
On the other hand, carbon blacks with smaller particle sizes around 15-25nm display better electrical conductivity. The higher surface area to volume ratio of smaller particles allows for increased contact points and easier movement of electrons. Therefore, smaller particle carbon blacks are preferred for applications requiring conductivity properties over reinforcement.
In terms of shape, carbon black particles can be spherical, irregular, or in a chain-like structure. Spherical particles provide uniform properties while irregular shapes offer better reinforcement. Chain-like or aggregated structures, where particles are fused together, result in even higher reinforcement abilities.
3. Surface Area and Purity
The surface area of carbon black refers to the total exposed area of its particles. Carbon black with a higher surface area means there is more surface for interaction with the compound it is mixed with, like rubber or plastic. This allows it to disperse well and more thoroughly mix at a molecular level. As a result, properties of the final material like reinforcement, conductivity and color development are enhanced.
However, if the surface area is too high, it can reduce the processability of the compound. Materials with extremely high surface area carbon black may not flow as well during processing steps like extrusion or molding. They can become stiff and difficult to manipulate. This affects the efficiency and quality of the manufacturing process.
Purity indicates the percentage of carbon content in the carbon black. Impurities refer to any other elements present along with carbon. Some amount of impurities is inevitable in the production process. But higher impurity levels could compromise the performance of the final product. Impurities may prevent the carbon black from properly interacting with the compound and realizing its reinforcing potential. It could lead to issues like reduced tensile strength or earlier failure of the material.
4. Source and Production Method
There are two main production methods used for making carbon black – furnace black and thermal black. In the furnace black process, carbon-containing raw materials like oil or natural gas are burned in a furnace with limited oxygen supply. This thermal decomposition leads to the formation of carbon black particles. Furnace black process is older and produces carbon blacks with a wide range of properties. The particles tend to have a more random, aggregated structure but higher purity levels due to refined feedstock and controlled combustion.
Thermal black or gas black production involves the cracking of hydrocarbon gases in a reactor at high temperatures using less oxygen compared to furnace process. Different types of thermal blacks are made by varying parameters like gas composition, temperature and residence time. This allows for a more controlled reaction and regulated particle structure like spherical or chain-like morphologies. Thermal blacks also have lower sulfur and ash content for many applications.
The source of raw material – be it oil, gas or recycled tires – influences the carbon black’s inherent characteristics. For example, carbon blacks from used tires have certain unique properties due to the presence of rubber in the feedstock. Understanding the production technique helps in comprehensive evaluation of the carbon black’s quality consistency and suitability for specific applications. A reputed manufacturer uses standardized production methods with strict quality controls to ensure specified carbon black properties are consistently delivered. This reliability is important from a performance and compliance perspective.
5. Reinforcing Ability
Carbon black’s capacity to reinforce is one of its most significant qualities. This is a reference to carbon black’s ability to improve the physical properties of materials it is combined with, such rubber or plastic. These matrices are strengthened and stiffened by carbon black, which enhances properties including modulus, abrasion resistance, and tensile strength.
The carbon black particles’ inherent properties determine their capacity to reinforce. Particle structure and size are important factors. Larger particle sizes of carbon blacks often offer superior reinforcing because they can create networks inside the compound and stop movement under stress more successfully. Excessively big particles, however, could result in poor dispersion. Reinforcement is also influenced by the shape of carbon black; spherical particles offer superior reinforcement compared to irregular or chain-like structures.
Moreover, larger surface area carbon blacks have stronger reinforcing properties. This is due to the fact that a larger surface area promotes more contact between the compound matrix and the surfaces of the carbon black particles. It promotes the development of stronger bonds and networks. The chemical makeup also plays a role because specific surface functional groups can enhance contact.
Conclusion
You may choose recovered carbon black continua systems that best suits your unique application needs and processing circumstances by weighing the aforementioned important considerations. The best solution for your needs will come from a choice that strikes a balance between important factors including sustainability, affordability, quality, and properties. For any extra advice on selecting the best recovered carbon black, speak with professionals in the field.